Today we will be bridging the gap between the Purchase and Sales Orders and dive into the Inventory Posting Profiles related to Production Orders.
We want D365 to automatically code the following journals.

Our focus continues to be on the configuration that enables synchronized, balanced Inventory sub-ledger vs. balanced Trial Balance general ledger, auto coded transactions.
Note: D365 allows you to pick or produce any Item Group.
We focus on picking Raw Materials and producing Finished Goods, not vice versa.
1. Chart of Accounts
General ledger > Setup > Chart of accounts > Main accounts
Create the following accounts.
Note: You can omit the accounts in gray as they do not relate directly to this session.
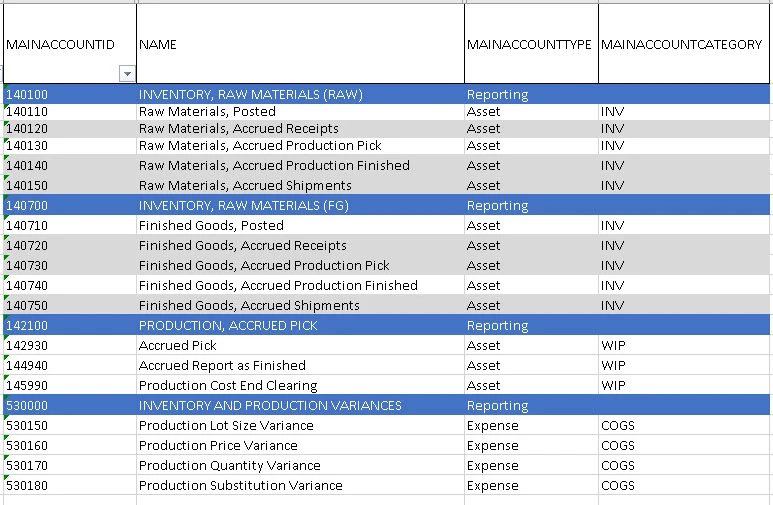
Inventory management > Setup > Inventory > Item groups
Add Item Groups:
RAW, Raw Materials
FG, Finished Goods
3. Pick List Journals
Inventory management > Setup > Posting > Posting [Production tab]
Pick List journals record the components for a produced item, lowering Inventory and increasing Production.
When a Pick List journal is posted, the following setups will automatically assign the Main Account in the journal.
Estimated Cost of Materials Consumed will credit Accrued Inventory for the value of the picked items.
Note: Main Accounts for the debit and credit both end with ####30.

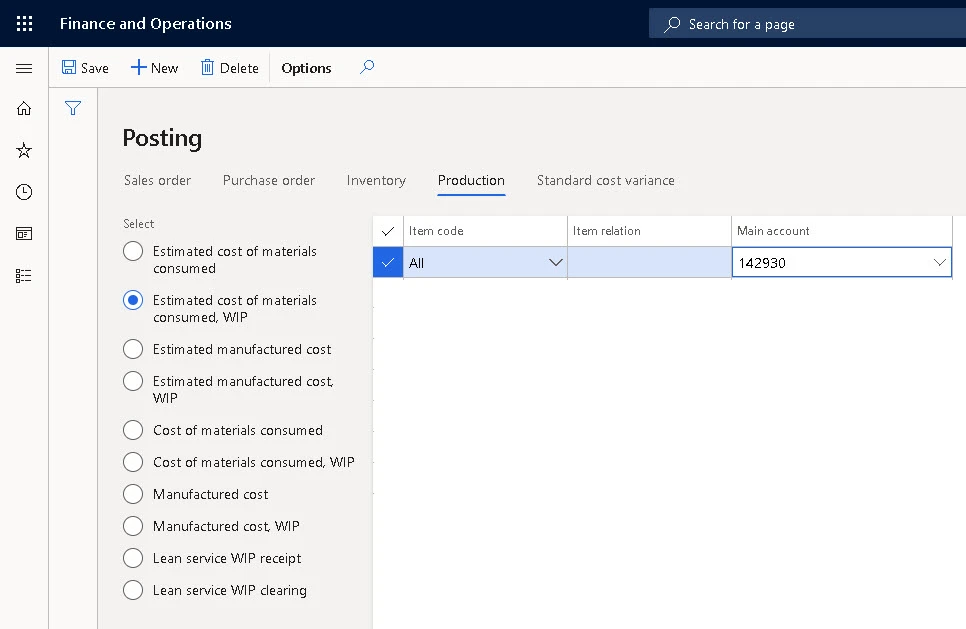
Inventory management > Setup > Posting > Posting [Production tab]
Report as Finished journals record the produced item (sum of components), lowering Production and increasing Inventory.
Even if the Production Order is still open, the items that have been Report as Finished may be sold on a Sales Order.
When a Report as Finished journal is posted, the following setups will automatically assign the Main Account in the journal.
Estimated Manufactured Cost will debit Accrued Inventory.
Note: Main Accounts for the debit and credit both end with ####40.
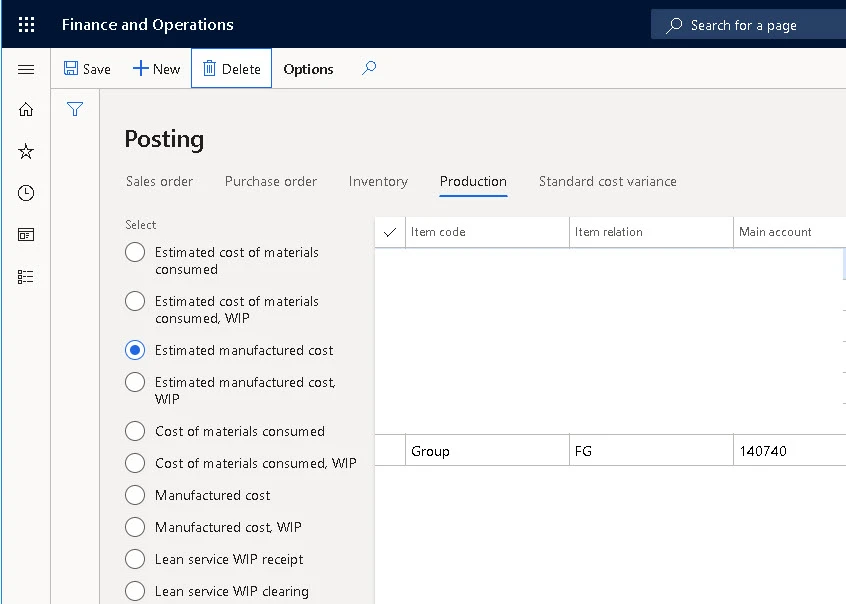

Inventory management > Setup > Posting > Posting [Standard Cost Variances tab]
Note: All Main Accounts assigned in this section begin with 530###.
Generally speaking, production variances will record mathematical differences from the Bill of Materials vs. the Production Cost journal (step 5).
Production Lot Size Variance
Variance is related to the differences between the standard cost calculation quantity and the production order quantity. The variance reflects the differences in the amortization of constant costs. The common sources for a lot-size variance include the following:
- The good quantity for a production order differs from the calculation quantity that is used in the standard cost calculation. The quantity provides the basis for amortizing constant costs.
- The value of constant costs in the production order differs from the constant costs that are used in the standard cost calculation. The constant costs in the production order can be different for several reasons. For example, the constant costs could reflect:
- Manual changes to the production bill of materials (BOM) or route.
- The selection of a different BOM version or route version when you are creating the production order.
- Planned engineering changes to the BOM version or route version that is assigned to the item.

Production Price Variance
Variance is related to the differences between the costs that were used for standard cost calculations during the start or estimation of the production order and the costs that were used for actual consumption transactions during the ending of the production order. The common sources for a production-price variance include the following:
- The cost category (and its cost-category price) for the reported consumption of a routing operation differs from the cost category that is used in standard cost calculation.
- The active cost for the cost-category price differs from the cost-category price that is used in standard cost calculation.
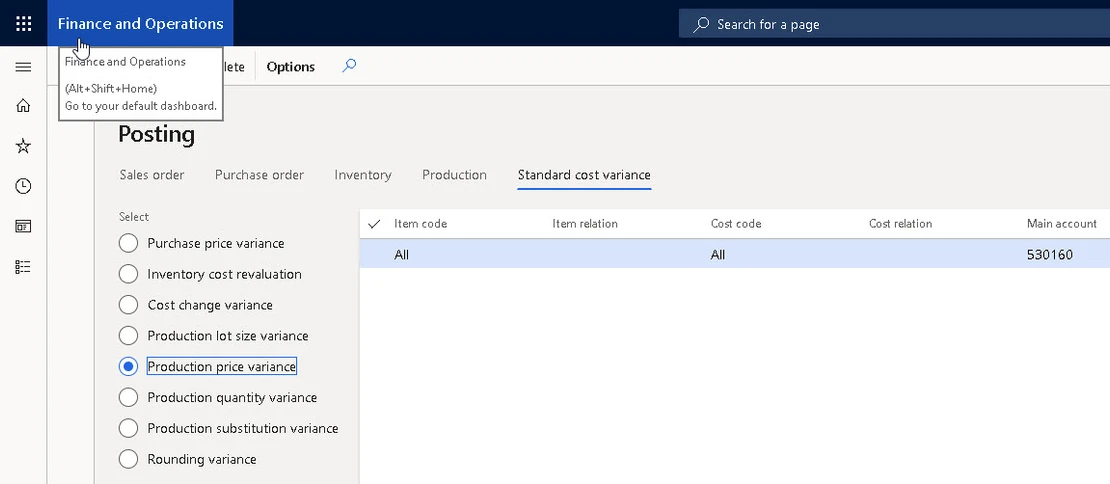
Production Quantity Variance
‘Variance that is related to the differences between the quantities for components and operations that were used for standard cost calculations and the quantities that were used for actual consumption transactions. The common sources for a production-quantity variance include the following:
- Over-issue a material component or under-issue a material component.
- Over-report time for a routing operation or under-report time for a routing operation.
- Over-receive or under-receive the good quantity of the parent item relative to the order quantity, but issue components and report operations completely, based on the order quantity for the production order.
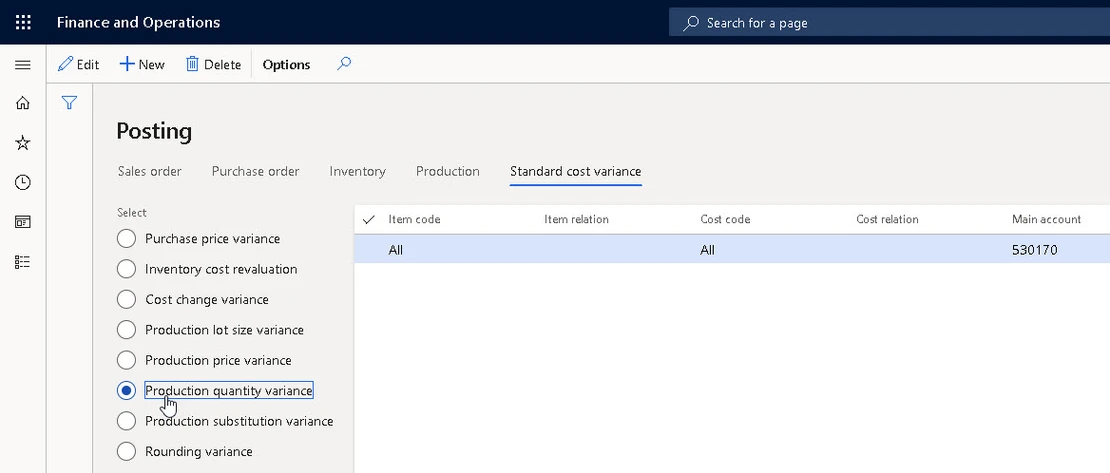
Production Substitution Variance
Variance that is related to the differences between the components and operations that were used for standard cost calculations and those that were used for actual consumption transactions. For example, the substitution variance could reflect actual consumption of a component that was not in the bills of material (BOM) for the standard cost calculation. The common sources for a production-substitution variance include the following:
- Issue a material component that is not in the production BOM.
- Add a component manually to the production BOM, and report it as consumed.
- Report an item as consumed, without adding it manually to the production BOM.
- Add an operation manually to the production route, and report it as consumed.
- Select a different BOM version when you are creating the production order, where the BOM version differs from the one that is used in the standard cost calculation.
- Select a different route version when you are creating the production order, where the route version differs from the one that is used in the standard cost calculation.

6. Production Cost Journal
Inventory management > Setup > Posting > Posting > [Production tab]
This is probably the most complex journal in D365. It reverses the Accrued Pick (step 3), reverses Accrued Report as Finished (step 4) journals, and posts the Financial Inventory values and Variances (step 5).
To simplify the processing a clearing account (145990) is utilized.
Cost of Materials Consumed will credit Financial Inventory for the picked items
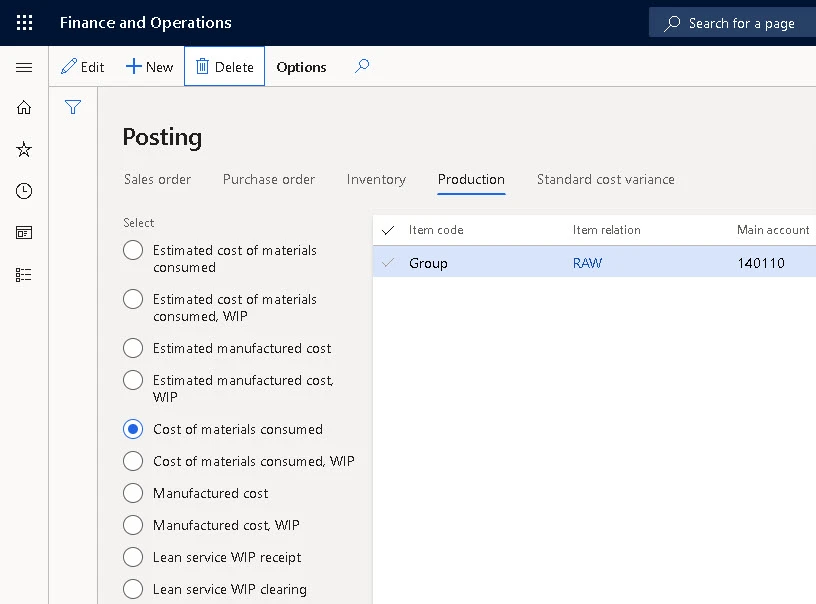

Note: Lines posted to the clearing account will add to zero.
Cost of Materials Consumed WIP will post to the clearing account (145990).

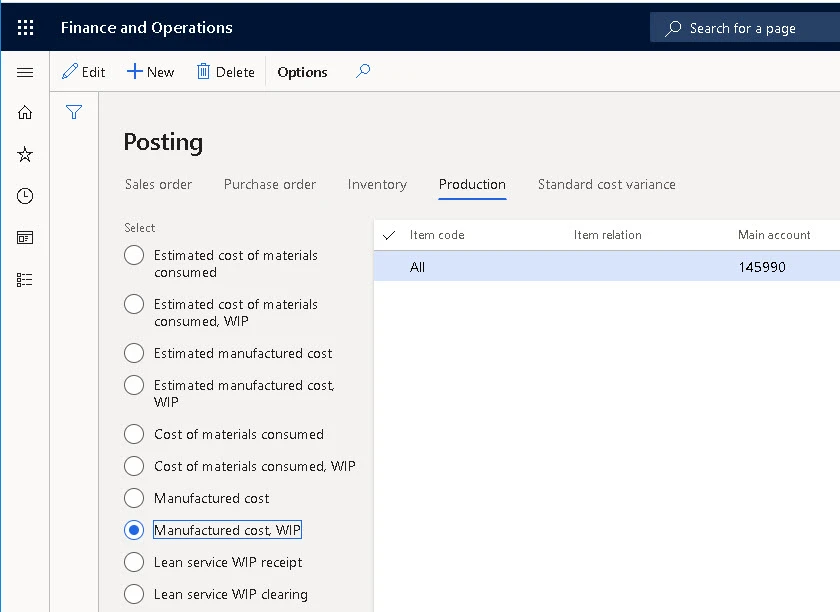